-
Magnesium Sacrificial Anodes
-
Magnesium Anodes Cathodic Protection
-
High Potential Magnesium Anode
-
Magnesium Ribbon Anode
-
Extruded Magnesium Anodes
-
Prepackaged Magnesium Anode
-
Water Heater Magnesium Anode
-
Wrought Magnesium Alloy
-
Magnesium Alloy Bar
-
High Strength Magnesium Alloy
-
Magnesium Alloy Sheet
-
Dissolvable Magnesium Alloy
-
Magnesium Rare Earth Alloy
-
FedererReliable quality of sacrificial magnesium anode.
-
AliceWell suited to our cathodic protection needs.
G97 Magnesium Alloy Bar Az91d Extruded Magnesium For Electronics
Place of Origin | CHINA |
---|---|
Certification | USA: G97,ASTM |
Minimum Order Quantity | 1000KGS |
Price | Negotiable |
Packaging Details | Pallet packing, or on customer's request |
Delivery Time | 30 Days after receiving the deposit |
Payment Terms | 50% Deposit , 50% Balance before deliver to the port |
Supply Ability | 500 mts per month |
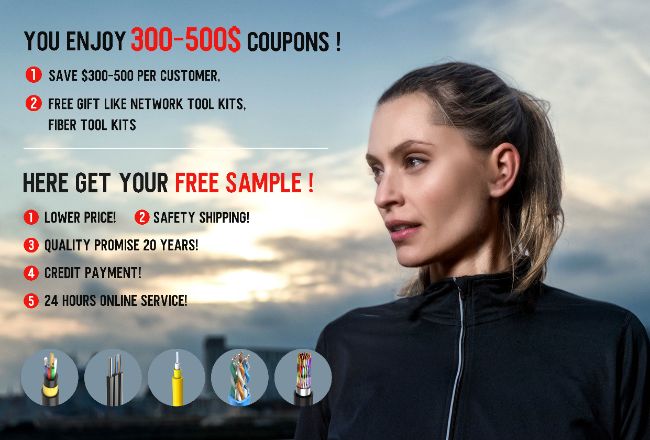
Contact me for free samples and coupons.
Whatsapp:0086 18588475571
Wechat: 0086 18588475571
Skype: sales10@aixton.com
If you have any concern, we provide 24-hour online help.
xKeywords | High Strength Magnesium Alloy | Feature | High Stiffness Ratio |
---|---|---|---|
Adventage | High Strength | Service | OEM / OEM |
Technical Standard | GB/T 17731-2015 | Application | Automobile Industry |
High Light | G97 Magnesium Alloy Bar,Magnesium Alloy Bar Az91d,Az91d Extruded Magnesium |
High Stiffness Ratio High Strength Magnesium Alloy Bar For Automobile Industry
Introduction:
High Strength Magnesium alloy bar has small, high specific strength, good electrical and thermal conductivity, corrosion resistance, beautiful shape, easy processing into density shape and other excellent performance, is widely used in aviation, aerospace, automotive, construction, electrical, chemical, machinery manufacturing and other industries. High strength magnesium alloy bar is an important structural material indispensable for many military and civil aircraft and transportation tools.
Features:
- Low density, the density of pure magnesium is only 1.74g/cm3, which is about 2/3 of aluminum and 1/4 of steel, close to the specific gravity of engineering plastics. It is the lightest structural alloy, which can effectively reduce the weight of components and save energy. energy consumption;
- The specific strength and specific stiffness are large, and the specific strength of magnesium alloys is not only higher than some high-strength steels, but even higher than aluminum alloys;
- Good thermal conductivity, large expansion coefficient, low elastic modulus, slightly inferior to general aluminum alloys, 300 times that of general engineering materials, and low temperature dependence, can be used to manufacture electronic products requiring good heat dissipation performance;
- It has good damping performance, strong absorption capacity and strong shock absorption, which can be used in situations with severe vibration, and can enhance the safety and comfort of automobiles when used in automobiles;
- Magnesium alloy is a non-magnetic shielding material with good electromagnetic shielding performance and strong anti-electromagnetic wave interference ability, which can be used in communication products such as mobile phones;
Processing performance advantage:
1. The melting cost is only 2/3 of that of aluminum:
2. Excellent die-casting formability: magnesium alloys can be die-casted to manufacture complex parts and ultra-thin shell parts, the thinnest can reach 0.45mm (ABS plastic is 1.2-2mm, aluminum alloy is 1.5-2mm), and the surface quality of magnesium castings and the The appearance is obviously better than that of aluminum: the affinity of magnesium die-casting with the mold is much lower than that of aluminum, and the life of the mold is more than twice that of aluminum.
3. The production efficiency of die casting is 25% higher than that of aluminum, metal mold casting is 300-500K higher than aluminum, and lost foam casting is 200% higher than aluminum.
4. Good cutting performance: magnesium alloy has low hardness and good cutting performance. The cutting resistance is only 56% of aluminum alloy and 43% of brass. High cutting speed and cheap cutting can be used for processing. Cutting tools, low tool consumption. And without grinding and polishing, you can get a very smooth surface with cutting fluid.
Application:
The automotive industry and the electronics industry have become the industries with the largest demand for magnesium alloys. The use of magnesium alloys in automobiles can reduce the weight by 20% to 25% compared with aluminum alloys. Magnesium alloy extrusions can be used in automotive bearing parts such as seat frames, window frames, chassis frames, wheel hubs, etc. Thin-wall magnesium alloy extruded pipe fittings are used in automobiles, and due to their small cross-sectional area, they can significantly reduce weight. Magnesium alloy sheets are used in the manufacture of outer panels for automotive body parts (such as doors, covers, guards, roof panels, etc.), which can greatly reduce the mass.
Photo: