-
Magnesium Sacrificial Anodes
-
Magnesium Anodes Cathodic Protection
-
High Potential Magnesium Anode
-
Magnesium Ribbon Anode
-
Extruded Magnesium Anodes
-
Prepackaged Magnesium Anode
-
Water Heater Magnesium Anode
-
Wrought Magnesium Alloy
-
Magnesium Alloy Bar
-
High Strength Magnesium Alloy
-
Magnesium Alloy Sheet
-
Dissolvable Magnesium Alloy
-
Magnesium Rare Earth Alloy
-
FedererReliable quality of sacrificial magnesium anode.
-
AliceWell suited to our cathodic protection needs.
Az80 High Strength Magnesium Alloy In Aircraft Bar Astm
Place of Origin | CHINA |
---|---|
Certification | USA: G97,ASTM |
Minimum Order Quantity | 1000KGS |
Price | Negotiable |
Packaging Details | Pallet packing, or on customer's request |
Delivery Time | 30 Days after receiving the deposit |
Payment Terms | 50% Deposit , 50% Balance before deliver to the port |
Supply Ability | 500 mts per month |
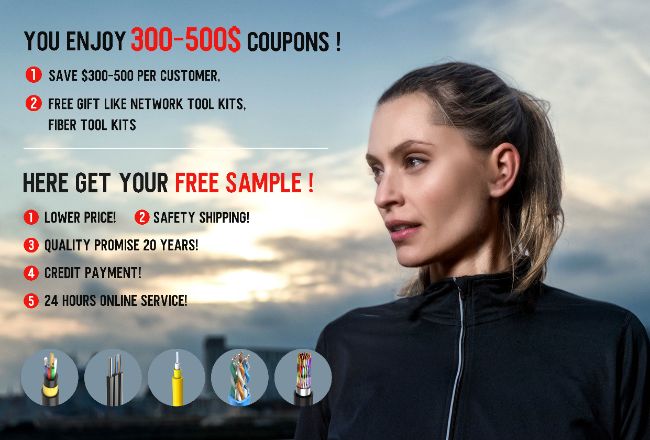
Contact me for free samples and coupons.
Whatsapp:0086 18588475571
Wechat: 0086 18588475571
Skype: sales10@aixton.com
If you have any concern, we provide 24-hour online help.
xKeywords | High Strength Magnesium Alloy | Feature | High Stiffness Ratio |
---|---|---|---|
Adventage | High Strength | Service | OEM / OEM |
Technical Standard | GB/T 17731-2015 | Application | Automobile Industry |
High Light | Az80 High Strength Magnesium Alloy,High Strength Magnesium Alloy Astm,Magnesium Alloy In Aircraft Bar Astm |
Resistant To Organic Corrosion High Strength Magnesium Alloy Bar For Automobile Industry
Introduction:
Compared with cast magnesium alloys, wrought magnesium alloys have greater development potential. Through the control of material structure and the application of heat treatment processes, wrought magnesium alloys can obtain higher strength, better ductility and more diverse mechanics. performance, so as to meet the application requirements of diverse engineering structural parts. Wrought magnesium alloys often need to be heated to a certain temperature and processed by hot forming techniques such as extrusion, rolling and forging.
Processing performance advantage:
1. The melting cost is only 2/3 of that of aluminum:
2. Excellent die-casting formability: magnesium alloy can be die-casting to manufacture complex parts and ultra-thin shell parts, the thinnest can reach 0.45mm, and the surface quality and appearance of magnesium castings are obviously better than those of aluminum: the affinity of magnesium die-castings with molds is much lower For aluminum, the mold life is more than twice that of aluminum.
3. The production efficiency of die casting is 25% higher than that of aluminum, metal mold casting is 300-500K higher than aluminum, and lost foam casting is 200% higher than aluminum
4. Good cutting performance: magnesium alloy has low hardness and good cutting performance, and the cutting resistance is only 56% of that of aluminum alloy and 43% of that of brass.
Application:
High-strength magnesium alloy bars have excellent properties such as small size, high specific strength, good electrical and thermal conductivity, corrosion resistance, beautiful appearance, and easy processing into dense shapes. They are widely used in aviation, aerospace, automobile, construction, electrical, chemical, and machinery manufacturing. and other industries. High-strength magnesium alloy bars are an indispensable and important structural material for many military and civil aircraft and vehicles.
Magnesium alloy die castings are mainly used to manufacture automobile instrument panels, seat frames, transmission housings, steering wheel control system components, engine parts, door frames, wheel hubs, brackets, clutch housings, body brackets, etc.
Photo: