-
Magnesium Sacrificial Anodes
-
Magnesium Anodes Cathodic Protection
-
High Potential Magnesium Anode
-
Magnesium Ribbon Anode
-
Extruded Magnesium Anodes
-
Prepackaged Magnesium Anode
-
Water Heater Magnesium Anode
-
Wrought Magnesium Alloy
-
Magnesium Alloy Bar
-
High Strength Magnesium Alloy
-
Magnesium Alloy Sheet
-
Dissolvable Magnesium Alloy
-
Magnesium Rare Earth Alloy
-
FedererReliable quality of sacrificial magnesium anode.
-
AliceWell suited to our cathodic protection needs.
0.02 Inch Extruded Magnesium Anodes G97 Magnesium Rod Water Heater
Place of Origin | CHINA |
---|---|
Certification | USA: G97,ASTM |
Minimum Order Quantity | 1000KGS |
Price | Negotiable |
Packaging Details | Pallet packing, or on customer's request |
Delivery Time | 30 Days after receiving the deposit |
Payment Terms | 50% Deposit , 50% Balance before deliver to the port |
Supply Ability | 500 mts per month |
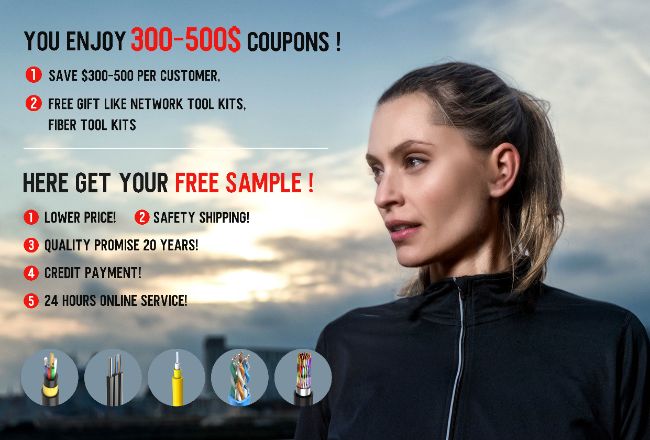
Contact me for free samples and coupons.
Whatsapp:0086 18588475571
Wechat: 0086 18588475571
Skype: sales10@aixton.com
If you have any concern, we provide 24-hour online help.
xKeywords | Extruded Magnesium Anode | Shape | Rod |
---|---|---|---|
Material | Magnesium Alloy | Product Technology | Extruded Magnesium Anode |
Usage | Anti-corrosion | Sample | Available |
Application | Cathodic Protection,water Heater | Surface | Smooth |
High Light | 0.02 Inch Extruded Magnesium Anodes,Extruded Magnesium Anodes G97,0.02 Inch Magnesium Rod Water Heater |
Continuous Drawing Production Process Extruded Magnesium Anode For Cathodic Protection
Introduction:
The high current output / weight ratio of the rod anode allows its wide application in the circumstance that demands small anode diameter and high cathodic current.
we provide two types of extruded magnesium alloy anode:Mg-Mn alloy with high potential and AZ31 alloy with standard potential.
Features:
The extruded magnesium alloy anode rod adopts a continuous drawing production process. The surface of the product is smooth, without pores and slag inclusions, the potential is greater than 1.48V, the efficiency is greater than 55%, and the bar yield is over 98%.
Chemical composition %:
Alloy | Al | Mn |
Zn (max) |
Ca (max) |
Si (max) |
Cu (max) |
Ni (max) |
Fe (max) |
Other Imp | |
each | total | |||||||||
AZ31B | 2.5-3.5 | 0.2-1.0 | 0.6-1.4 | 0.04 | 0.10 | 0.01 | 0.001 | 0.005 | --- | 0.30 |
Mg-Mn | 0.01max | 0.5-1.3 | --- | --- | --- | 0.02 | 0.001 | 0.03 | 0.05 | 0.30 |
Extruded rod anodes size specification:
Diameter (inch) |
Core eccentric (inch) |
Core diameter (inch) |
Straightness (inch/2 ft length) |
Weight (1bs/inch) |
Magnesium Extruded rod | ||||
0.675-0.020 | 0.050 | 0.135 | 0.060 | 0.025 |
0.750-0.020 | 1/16 | 0.135 | 0.040 | 0.031 |
0.800-0.020 | 1/16 | 0.135 | 0.040 | 0.035 |
0.840-0.020 | 1/16 | 0.135 | 0.040 | 0.038 |
0.900-0.020 | 1/16 | 0.135 | 0.040 | 0.043 |
1.050-0.020 | 1/16 | 0.135 | 0.040 | 0.057 |
1.315-0.020 | 1/16 | 0.135 | 0.040 | 0.089 |
Production Process:
1. Casting equipment
The use of high-power resistance furnace can realize automatic temperature control, and the efficiency of stretching equipment is greatly improved.
2. Melting and pouring process
Ingredients: According to the requirements of alloy composition, the required amount of master alloys, magnesium ingots, zinc ingots, aluminum ingots, bar sawing heads and other returning materials should not exceed 10% of the total charge.
Feeding and smelting: Check the crucible according to the regulations. After meeting the requirements, power on the resistance furnace, preheat the crucible to 400~500℃, and evenly sprinkle a layer of powder RJ-2 flux on the bottom and inner wall of the crucible. Then the charge preheated to above 150°C is added in sequence. The addition of the charge should be placed as densely as possible to narrow the gap between the charges. Then gradually increase the temperature. When 1% of the total charge is melted, the furnace temperature is adjusted to 730 °C for metamorphism treatment, and samples are taken for fracture inspection.
The key to adopting the low-pressure oxygen-free pouring process is the coordination and synchronization of pouring speed, stretching speed and cooling water volume. Otherwise, there will be undercasting and breakage of the stretch rod.
3. Inspection and sawing
After the drawn bar products pass the sawing gate and the appearance inspection, the necessary heat treatment is carried out in the heat treatment furnace, and then the second sawing is performed according to the length required by the user.
Photos: