-
Magnesium Sacrificial Anodes
-
Magnesium Anodes Cathodic Protection
-
High Potential Magnesium Anode
-
Magnesium Ribbon Anode
-
Extruded Magnesium Anodes
-
Prepackaged Magnesium Anode
-
Water Heater Magnesium Anode
-
Wrought Magnesium Alloy
-
Magnesium Alloy Bar
-
High Strength Magnesium Alloy
-
Magnesium Alloy Sheet
-
Dissolvable Magnesium Alloy
-
Magnesium Rare Earth Alloy
-
FedererReliable quality of sacrificial magnesium anode.
-
AliceWell suited to our cathodic protection needs.
Shock Absorption Wrought Magnesium Alloy Az91 Damping ASTM
Place of Origin | CHINA |
---|---|
Certification | USA: G97,ASTM |
Minimum Order Quantity | 1000KGS |
Price | Negotiable |
Packaging Details | Pallet packing, or on customer's request |
Delivery Time | 30 Days after receiving the deposit |
Payment Terms | 50% Deposit , 50% Balance before deliver to the port |
Supply Ability | 500 mts per month |
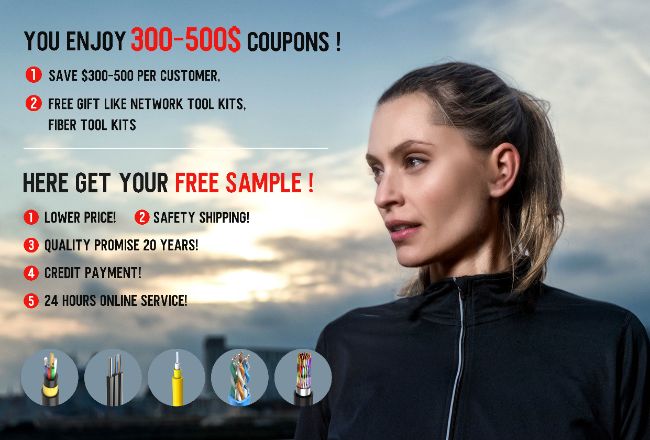
Contact me for free samples and coupons.
Whatsapp:0086 18588475571
Wechat: 0086 18588475571
Skype: sales10@aixton.com
If you have any concern, we provide 24-hour online help.
xKeywords | Wrought Magnesium Alloy | Material | Add Other Elements Based On Magnesium |
---|---|---|---|
Feature | Damping And Shock Absorption | Service | OEM / OEM |
Technical Standard | GB/T 17731-2015 | Application | Automobile Industries |
High Light | Wrought Magnesium Alloy ASTM,Shock Absorption Wrought Magnesium Alloy,Magnesium Alloy Az91 Damping |
Damping And Shock Absorption Wrought Magnesium Alloy For Automobile Industries
Introduction:
Magnesium alloy has the characteristics of low density, high specific strength and specific stiffness, good dimensional stability, good thermal conductivity and electrical conductivity, vibration absorption and easy processing and forming, so magnesium alloy is one of the competitive automotive wheel quantization materials.
At present, most of the parts made of magnesium alloys in automobiles are die castings. Magnesium alloy die castings are the lightest among all die casting alloys and have a longer service life than aluminum alloys.
Magnesium alloy die-casting parts are mainly used to produce automobile instrument panels, seat frames, transmission housings, steering wheel control system components, engine parts, door frames, wheel hubs, brackets, clutch housings, body brackets, etc.
Features:
Magnesium alloys are alloys based on magnesium and other elements. Its characteristics are: low density (about 1.8g/cm3), high strength, large elastic modulus, good heat dissipation, good shock absorption, larger impact load capacity than aluminum alloy, and good corrosion resistance to organic substances and alkalis. The main alloying elements are aluminum, zinc, manganese, cerium, thorium and a small amount of zirconium or cadmium.
Application:
High-performance magnesium alloys are excellent aerospace materials. For example, the magnesium alloy (AZ31) matrix composite material with silicon carbide whiskers (20% by volume) as the strengthening phase, its elastic modulus is increased by 10%, and the strength is increased to about 450MPa; the United States has used magnesium alloy composite materials to manufacture propellers, For missile tails, etc., naval satellites have used magnesium alloy composite materials for structural parts such as brackets, bushings, and beams, and their comprehensive performance is better than that of aluminum-based composite materials.
Main physical and mechanical properties of commonly used structural materials:
magnesium casting | Magnesium forgings | Aluminum casting | Aluminum forgings | cast iron | copper | Engineering plastics | |||||
Alloy model | AZ91 | AM50 | AZ80 | AZ31-H24 | A380 | A356-T6 | 6061-T6 | 5182-H24 | HT350 | Galvanized sheet | ABS |
Preparation method | die casting | die casting | squeeze | plate | die casting | permanent film | squeeze | plate | sand mold | plate | - |
Density (g/cm³) | 1.81 | 1.77 | 180 | 1.77 | 2.68 | 2.76 | 2.70 | 2.70 | 7.15 | 7.8 | 1.07 |
Elastic Modulus (GPa) | 45 | 45 | 45 | 45 | 71 | 72 | 69 | 70 | 100 | 210 | 2.1 |
Tensile strength (MPa) | 240 | 210 | 380 | 290 | 324 | 262 | 310 | 310 | 293 | 390 | 43 |
Yield strength (MPa) | 160 | 125 | 275 | 220 | 159 | 186 | 275 | 235 | 320 | 39 | |
Elongation(%) | 7 | 15 | 7 | 15 | 5 | 12 | 8 | 0 | 26 | 16.5 |
Photos: